Cylindrical Cell Pilot Equipment: Key Tools for Battery Prototyping
Cylindrical cell pilot equipment is a specialized suite of tools and machines designed to produce cylindrical batteries at a pilot scale. These batteries, commonly used in electric vehicles (EVs), portable electronics, and energy storage systems, require precise fabrication techniques to ensure performance and safety.
Pilot equipment bridges the gap between laboratory research and mass production, allowing for the development, testing, and optimization of cylindrical battery designs.
---
● Core Processes in Cylindrical Cell Pilot Production
1. Electrode Preparation
- Fabricating high-quality anode and cathode electrodes by coating active materials on metal foils (e.g., copper for anodes and aluminum for cathodes).
2. Electrode Assembly
- Cutting, winding, and assembling the electrodes with separators into a cylindrical structure.
3. Cell Sealing
- Sealing the cell components within a cylindrical casing, typically made of steel or aluminum.
4. Electrolyte Filling
- Injecting electrolyte into the sealed cell under controlled conditions.
5. Formation and Aging
- Performing the initial charge/discharge cycles to stabilize the cell's chemistry.
6. Testing and Quality Control
- Evaluating cell performance, safety, and consistency through rigorous testing.
---
● Key Cylindrical Cell Production Plant
● 1. Electrode Fabrication Equipment
- Slurry Mixer: Prepares a uniform slurry by mixing active materials, binders, and solvents.
- Coating Machine: Applies the slurry onto current collector foils with high precision.
- Drying Oven: Removes solvents from the coated foils.
- Calendaring Machine: Compresses electrodes to achieve uniform thickness and density.
- Electrode Cutting Machine: Cuts the foils into precise shapes for assembly.
● 2. Cell Assembly Equipment
- Electrode Winding Machine: Rolls the anode, separator, and cathode into a jelly roll structure.
- Tab Welding Machine: Welds tabs onto electrodes to establish electrical connections.
- Cylindrical Can Sealing Machine: Seals the jelly roll and tabs inside the metal casing.
● 3. Electrolyte Filling and Sealing
- Electrolyte Filling Machine: Precisely injects the electrolyte into the cylindrical cell.
- Vacuum Sealing Machine: Ensures an airtight seal after electrolyte filling.
● 4. Formation and Aging Systems
- Formation Racks: Perform initial charging and discharging cycles under controlled conditions.
- Aging Cabinets: Store cells in a controlled environment to stabilize performance.
● 5. Testing and Quality Control Machines
- Impedance Tester: Measures internal resistance.
- Capacity Tester: Evaluates the charge/discharge capacity.
- Safety Testing Equipment: Conducts short circuit, drop, and thermal runaway tests.
---
● Advantages of Cylindrical Cell Pilot Equipment
1. Scalability
- Allows for smooth transition from small-scale lab production to industrial-scale manufacturing.
2. Process Optimization
- Enables testing and refinement of electrode formulations, assembly techniques, and cell designs.
3. Cost-Effective R&D
- Pilot equipment reduces material waste and production costs during development.
4. Customization
- Flexible configurations to produce different cell sizes (e.g., 18650, 21700, 4680).
5. Quality Assurance
- Ensures that prototype cells meet performance and safety standards before mass production.
---
● Common Cylindrical Cell Sizes Produced
1. 18650 Cells
- Widely used in consumer electronics and early EV battery packs.
2. 21700 Cells
- Higher energy density and improved thermal management, common in EVs and power tools.
3. 4680 Cells
- Larger format with higher capacity and lower production costs, gaining traction in modern EVs.
---
● Applications of Cylindrical Cell Pilot Equipment
1. Electric Vehicles (EVs)
- Prototyping cells for automotive applications.
2. Renewable Energy Storage
- Developing high-capacity cells for grid storage and backup systems.
3. Consumer Electronics
- Testing battery designs for laptops, cameras, and handheld devices.
4. Medical Devices
- Creating cells for portable medical equipment.
---
● Considerations When Selecting Cylindrical Cell Pilot Equipment
1. Compatibility with Cell Types
- Ensure the equipment supports the desired cylindrical cell sizes and chemistries (e.g., Li-ion, LFP).
2. Automation Level
- Opt for manual, semi-automated, or fully automated systems based on production scale.
3. Precision and Repeatability
- High precision in electrode cutting, winding, and filling ensures consistent cell performance.
4. Scalability
- Equipment should be adaptable for scaling up to higher production volumes.
5. Safety Standards
- Machines must comply with safety protocols for handling hazardous materials like lithium and electrolytes.
---
● Challenges in Cylindrical Cell Pilot Production
1. Material Waste
- Inefficient processes can lead to higher material losses during prototyping.
2. Equipment Cost
- High-precision machines require significant upfront investment.
3. Process Complexity
- Achieving uniformity in electrode coating and assembly can be challenging.
4. Safety Risks
- Handling flammable and reactive materials necessitates stringent safety measures.
---
● Conclusion
Cylindrical cell pilot equipment is an essential component of modern battery development, enabling manufacturers to create and refine cells for diverse applications. With advanced tools for every stage of production, from electrode fabrication to formation and testing, these systems offer unparalleled precision and scalability. Investing in high-quality pilot equipment ensures that the transition to full-scale manufacturing is efficient, cost-effective, and aligned with performance standards.
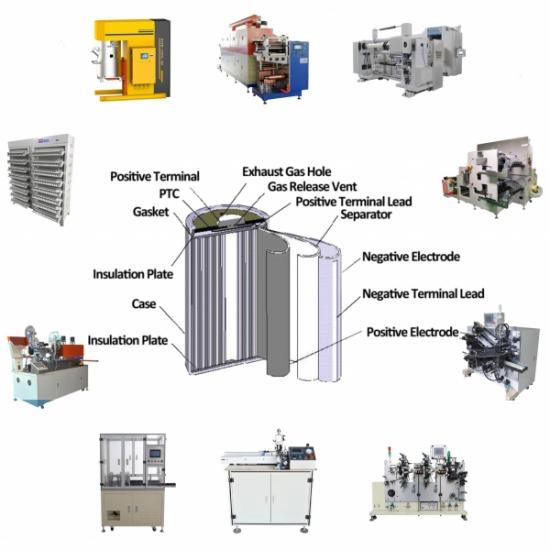