Prismatic Cell Fabrication Line: Overview and Key Processes
A prismatic cell fabrication line is a specialized production setup designed to manufacture prismatic lithium-ion battery cells. These cells are characterized by their flat, rectangular shape, which allows for efficient space utilization in battery packs, making them popular in applications such as electric vehicles (EVs), energy storage systems, and consumer electronics.
●Key Processes in Prismatic Cell Fabrication
1.Material Preparation
-Electrode Materials: Active materials for both the anode and cathode are mixed with binders and conductive additives to create slurries.
-Separator Production: Separators made from materials like polyethylene or polypropylene are prepared to prevent short circuits between the electrodes.
2.Electrode Coating
- The slurry is coated onto metal foils (copper for anodes and aluminum for cathodes) using precision coating machines, ensuring a uniform thickness essential for performance.
3.Drying and Calendering
- Coated electrodes are dried to remove solvents and then calendered to compress the materials, enhancing density and conductivity.
4.Cutting and Slitting
- After drying, electrodes are cut or slit into precise dimensions suitable for the prismatic cell design, ensuring uniformity for assembly.
5.Cell Assembly
-Layer Stacking: The cut anode, separator, and cathode layers are stacked in a specific order within a prismatic cell casing.
-Electrolyte Filling: Electrolyte is injected to saturate the electrodes and separator.
-Sealing: The cell is sealed using methods like heat sealing or ultrasonic welding to prevent leakage and contamination.
6.Formation and Aging
- The assembled cells undergo formation, where they are charged and discharged to stabilize their chemistry. This step is crucial for ensuring reliability and performance.
7.Quality Control and Testing
- Rigorous testing is conducted to assess various performance metrics, including capacity, cycle life, and safety. This ensures that the cells meet industry standards.
●Key Equipment in a Prismatic Cell Production Plant
1.Mixers and Coaters: For preparing and applying electrode slurries.
2.Drying Ovens: To remove solvents from coated electrodes.
3.Calendering Machines: For compressing electrodes to desired specifications.
4.Cutting and Slitting Machines: For precise sizing of electrodes.
5.Cell Assembly Stations: Automated or manual setups for stacking, filling, and sealing cells.
6.Battery Testing Systems: For conducting performance and safety tests.
●Advantages of Prismatic Cells
1.Space Efficiency: Their flat shape allows for efficient packing in battery systems, optimizing space in applications like EVs.
2.Scalability: Prismatic cells can be manufactured in various sizes and capacities, making them adaptable to different applications.
3.Thermal Management: Their design can facilitate better thermal management, enhancing safety and performance.
●Applications of Prismatic Cells
-Electric Vehicles: Widely used in EV battery packs for their high energy density and efficient design.
-Energy Storage Systems: Suitable for large-scale energy storage applications, supporting renewable energy integration.
-Consumer Electronics: Employed in devices requiring compact, high-capacity batteries.
●Conclusion
Automatic Prismatic Cell Production Line is integral to the production of advanced lithium-ion batteries that support a variety of applications. By streamlining processes and implementing rigorous quality control, these lines ensure the efficient and reliable production of prismatic cells. As the demand for energy storage solutions continues to rise, the evolution and optimization of prismatic cell manufacturing will play a critical role in the future of energy technology.
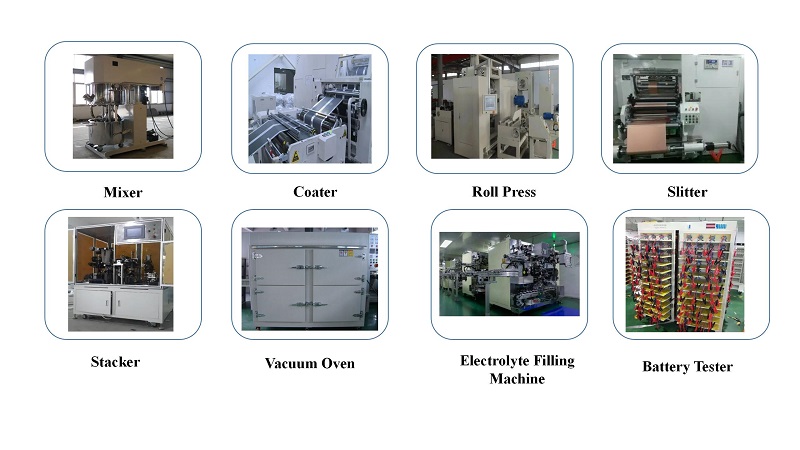